TDK Front Line
Vol.2 Taking the Lead in Commercializing the World’s First SMD-Type All-Solid-State Battery
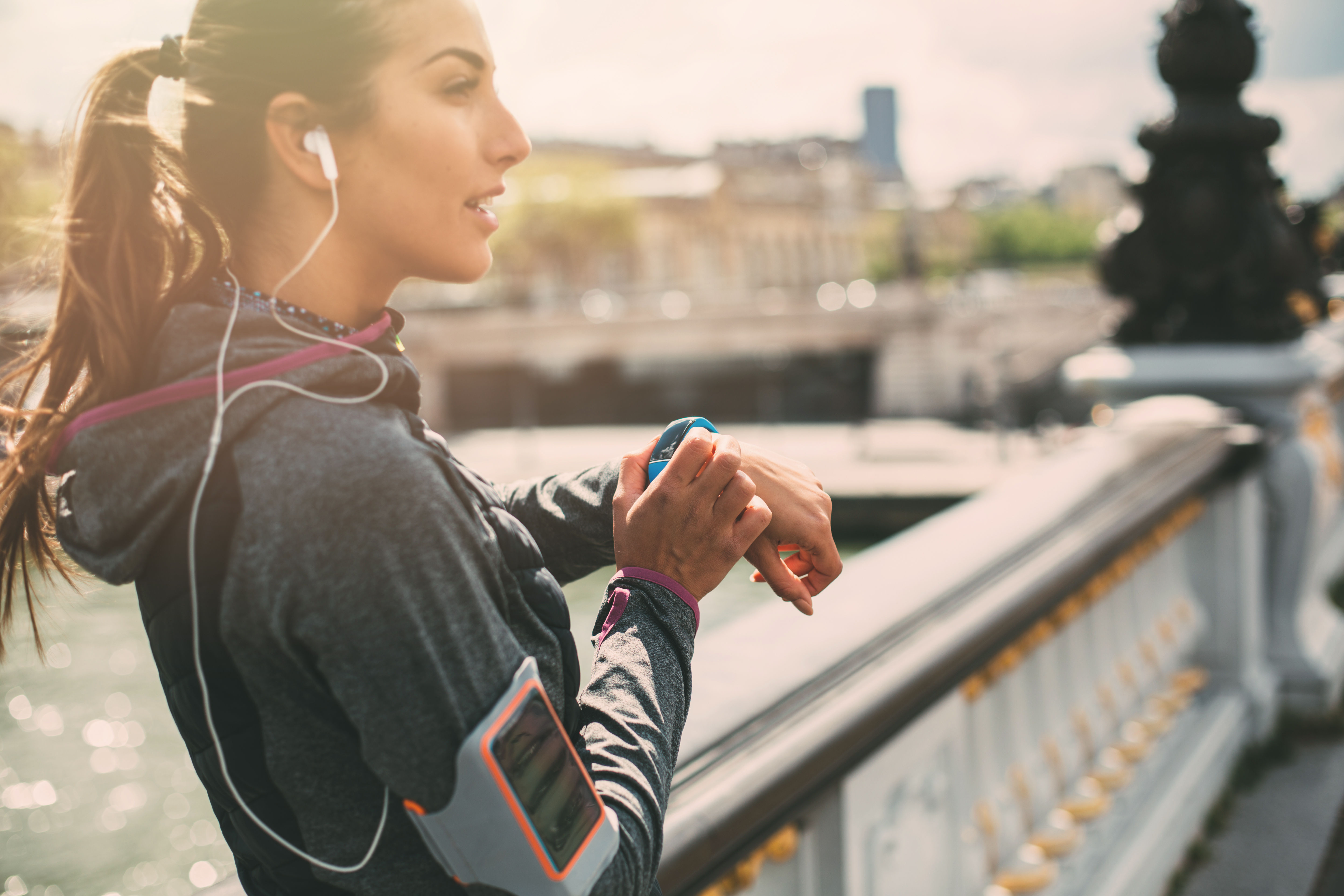
All-solid-state battery research and development has progressed worldwide in the aim of creating next-generation secondary rechargeable and dischargeable batteries to replace existing lithium ion batteries. The use of non-flammable solid-state electrolytes instead of liquid electrolytes eliminates the risk of leakage liquid spill and fire, and ensures outstanding safety and reliability as well as long life. In 2017, TDK commercialized a ground-breaking world’s first SMD-type all-solid-state lithium ion secondary battery called “CeraChargeTM” that harnessed ceramic materials technology, layering technology, and sintering technology obtained through production of multilayer electronic components. Combining this battery with wearable devices, which require smaller power supply, and Bluetooth beacon, and together with other energy-harvesting technologies enables IoT devices that do not depend on external power supply or require battery replacement.
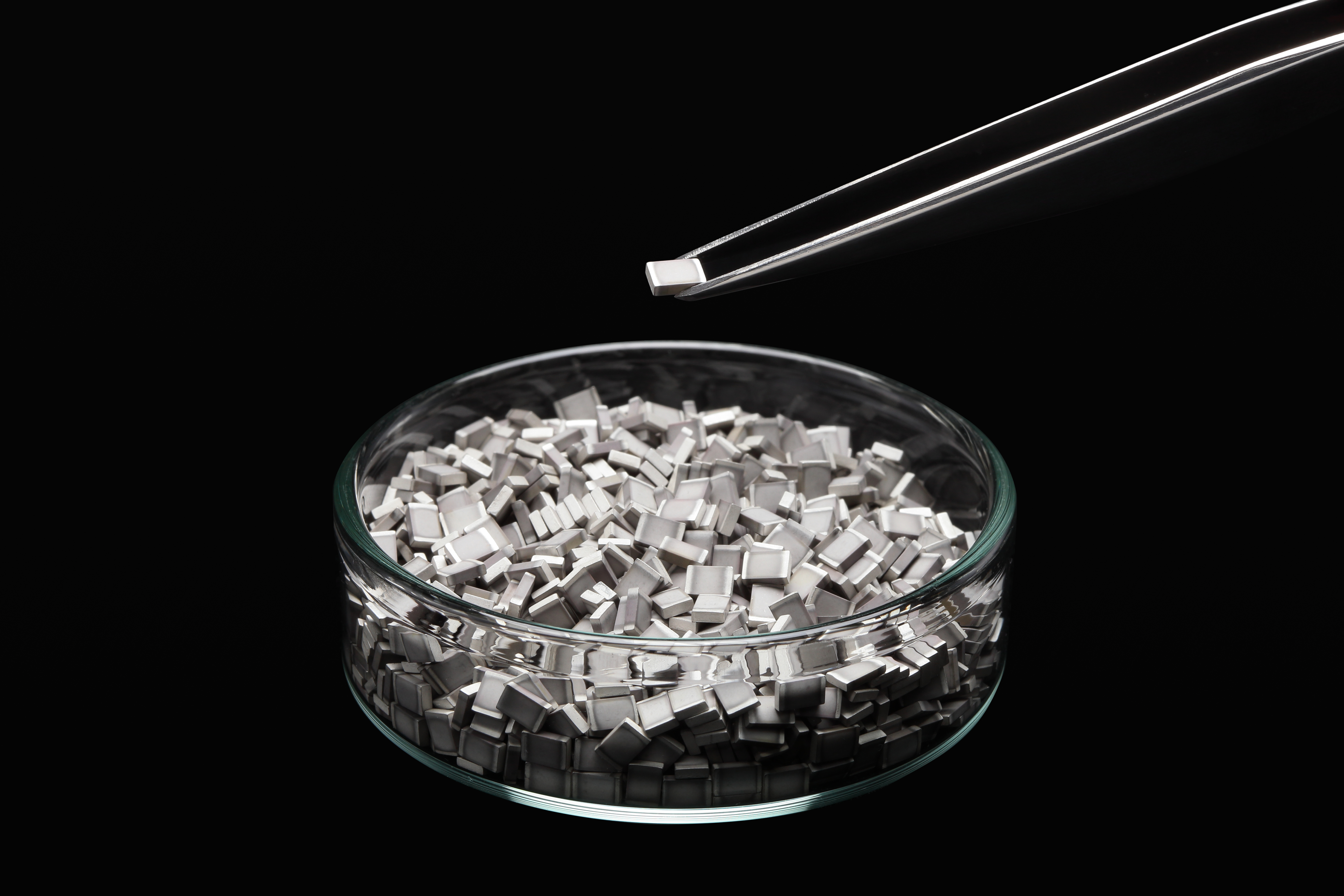
- Innovative Secondary Battery Using Solid-State Electrolyte Instead of Liquid Electrolyte
- Chargeable and Dischargeable All-Ceramic Battery that Can Be Mounted on a Board Together with Chip Components
- TDK Technology Realizes the World’s First Solid SMD Battery, CeraChargeTM
- Use Anticipated in Various Applications, Including IoT Devices
- Development Under Way for Next-Generation Products with Higher Capacity and Voltage
Innovative Secondary Battery Using Solid-State Electrolyte Instead of Liquid Electrolyte
After discovering electromagnetic induction in 1831, the renowned experimental scientist Michael Faraday studied electrolysis, and in 1833 the outcomes of his research became established as Faraday's Laws of Electrolysis. Electrochemical terms including electrode, electrolyte, ion, anode, and cathode were originated and introduced around that time.
An electrolyte is a material that is ionized into cations and anions when dissolved in a solvent such as water, and the solution becomes electrically conductive. A battery transforms chemical energy into electrical energy by using the property of ions to move electrical charges via an electrolyte. Batteries that are discharged and not rechargeable are called primary batteries, and rechargeable batteries are called secondary batteries.
Lithium ion batteries are an innovative type of secondary battery, first commercialized in 1991 by the efforts of Japanese researchers. Offering extremely high energy density, they have been used for notebook PCs, smartphones, and other mobile devices, swiftly cornering the market. Increasingly, they are being used as the main battery for electric vehicles (EVs).
However, lithium ion batteries use flammable liquid organic solvent as an electrolyte, resulting in risk of liquid spill, fire, etc. All-solid-state lithium ion secondary batteries (hereinafter abbreviated to “all-solid-state batteries”) using a non-flammable solid electrolyte have attracted worldwide attention as a new type of secondary battery offering a fundamental solution to these problems. The diagram below shows the differences in mechanism between a conventional lithium ion battery and an all-solid-state battery.
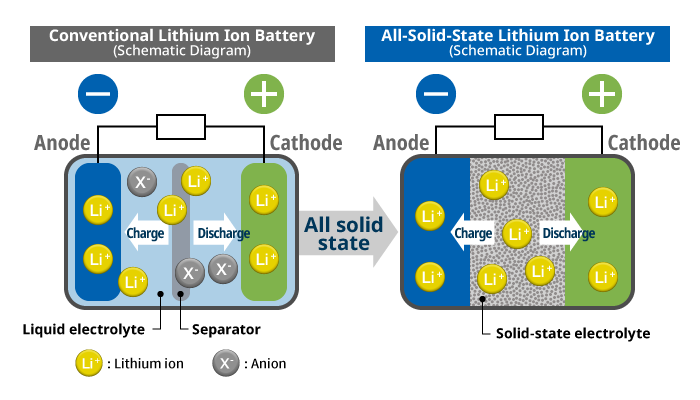
Chargeable and Dischargeable All-Ceramic Battery that Can Be Mounted on a Board Together with Chip Components
Compared with conventional lithium ion batteries, all-solid-state batteries have the following advantages:
Advantages of all-solid-state batteries
● The use of a solid electrolyte instead of a liquid electrolyte eliminates problems such as liquid spill and fire, and ensures high levels of safety and reliability.
● A separator to divide positive and negative electrodes is not required.
● In a lithium ion battery, lithium ions and anions move in a liquid electrolyte. However, in an all-solid-state battery, only lithium ions move in a solid electrolyte, and thus secondary reactions (oxidization of anions, dissolution of solvent molecules, etc.) rarely occur, ensuring long life.
● Wide operating temperature range.
● The large capacity of a conventional lithium ion battery is achieved by connecting many electric cells. In an all-solid-state battery, capacity can be increased by layering electrodes and solid electrolytes. Therefore, when large capacity is not required and/or when space on a circuit board is limited, an SMD-type all-solid-state battery is more suitable than a lithium ion battery. Connecting multiple all-solid-state batteries in series or parallel enables increases in voltage and capacity.
Types of solid electrolyte
Two main types of solid electrolytes are used for all-solid-state batteries: sulfide electrolytes and oxide electrolytes.
Sulfide electrolytes have relatively high ion conductivity and are likely to be used for EV drive batteries. However, they do require safety measures, since sulfur is included in solid electrolytes, and it generates toxic hydrogen sulfide (H2S) when it reacts with water.
Oxide electrolytes, on the other hand, do not generate hazardous substances and are safer than sulfide electrolytes. They are likely to be used for compact secondary batteries necessary for wearable devices and IoT devices.
CeraChargeTM, a world-leading all-solid-state battery commercialized by TDK, is an SMD-type secondary battery using proprietary lithium-based oxide (ceramics). Its inner structure is shown in the diagram below.
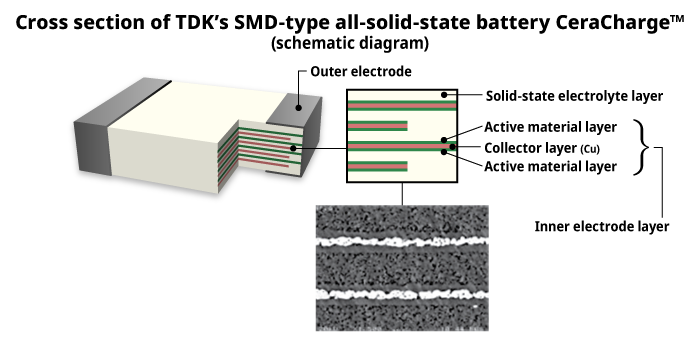
TDK Technology Realizes the World’s First Solid SMD Battery, CeraChargeTM
When considering electrolysis and electroplating, it is easy to understand that current flows by movement of ions in a liquid electrolyte, but more difficult to imagine that ions move in a solid substance. In fact, many electrolytes are insulated in a solid substance. Since an electrolyte has a dense structure in which cations and anions are systematically arrayed, it is difficult not only for ions, but also for electrons to move in a solid substance.
However, it has long been known that some solid electrolytes have ion conductivity, and they have been used for devices such as gas sensors. When an opening is created in the dense structure due to a lattice defect, ions can move by using the opening as a path. To use this solid electrolyte for a battery, however, it needs to have higher ion conductivity.
Practical use of all-solid-state batteries requires solving the following technical problems:
Problem (1): Quest for a solid electrolyte with high ion conductivity
One of the disadvantages of solid electrolytes is that the ion conductivity is lower than that of liquid electrolytes used for conventional lithium ion batteries by a factor of 1-2 digits. Recently, however, solid electrolytes with ion conductivity close to that of liquid electrolytes have been found. TDK has adopted proprietary lithium-based oxide as a solid electrolyte and electrode active substance, and commercialized a compact SMD-type all-solid-state battery, CeraChargeTM, that has relatively high energy density.
Problem (2): Reduction of inner resistance
Another technical problem of all-solid-state batteries is high inner resistance. Interface resistance between an electrode active material and solid electrolyte is a particular problem. A key technological challenge is how to form a low-resistance interface without using liquid. Moreover, there is a need to lower intergranular resistance by controlling the material composition and/or grain diameter of ceramic grains.
Problem (3): Reliability improvement and cost reduction
CeraChargeTM is manufactured at TDK’s factory in Austria, which has superb technology for producing multilayer electronic components. CeraChargeTM is manufactured with the sheet construction method for multilayer electronic components. However, since it has a lot of components, the print, layering, sintering, and inspection processes are more complicated than MLCC, and extremely advanced technology is adopted for each process.
Widespread deployment of all-solid-state batteries also requires improved reliability and lower costs. Copper (Cu) is used as a current collector for CeraChargeTM. Precise heat process control technology is required in order to sinter the copper current collector layer, ceramic active material layer, and solid electrolyte at the same time. Our factory in Austria has manufactured many multilayer products with internal copper electrodes, and its technology and know-how were applied to commercializing the world’s first solid SMD battery, CeraChargeTM.
Use Anticipated in Various Applications, Including IoT Devices
CeraChargeTM is a solid-state SMD battery with an EIA1812 package size (4.5 x 3.2 mm), rated voltage of 1.4 V, and capacity of 100μAh. The voltage and capacity can be increased by connecting the batteries in series or parallel. Use of CeraChargeTM is anticipated in various applications such as real time clocks (RTCs), Bluetooth beacon transmission, and IoT devices.
Sample application (1): Backup power for RTCs
RTCs are built-in clocks or IC functions in PCs and digital home appliances. A coin cell or similar battery is used so that RTCs function even when system power is off. However, when the battery runs out, it needs to be replaced. As shown in the diagram below, the use of CeraChargeTM eliminates troublesome replacement of batteries, and even if system power is turned off, the RTC function can provide backup for approximately 1 to 2 weeks.
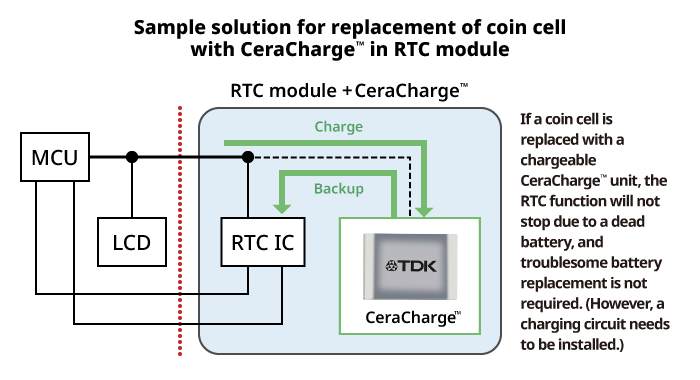
Sample application (2): BLE beacon using solar power
A Bluetooth Low Energy (BLE) beacon is a system that detects and sends information on the positions of the user or objects using the Bluetooth radio wave. This system has been used for guides to stores, facilities, and other premises. Low power consumption is one feature of BLE. Combining solar batteries, CeraChargeTM, and a capacitor (MLCC/EDLC) enables constant operation of a BLE beacon without using a primary battery, which would require replacement, or external power supply. The diagram below shows a solar power BLE beacon drive model. Power generated by solar batteries first charges the capacitor, which is the main power supply, and then charges CeraChargeTM, which is a subsidiary power supply. When the energy stored in the capacitor is consumed, CeraChargeTM charges the capacitor. With this cycle, a BLE beacon operates constantly. In systems with many BLE beacons installed, labor and cost of battery replacement are significantly reduced.
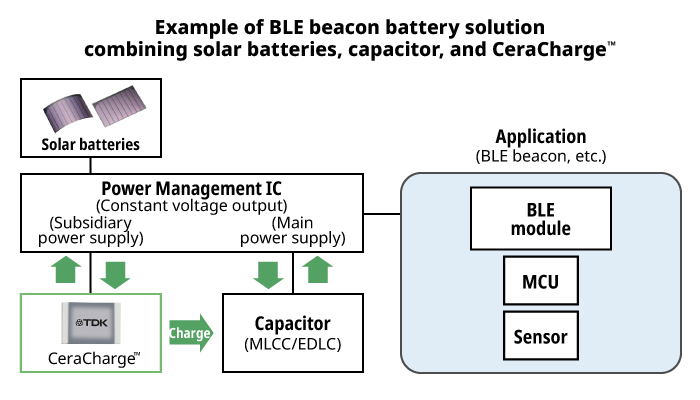
Development Under Way for Next-Generation Products with Higher Capacity and Voltage
One of the features of CeraChargeTM is that it can be charged by energy harvesting from environmental sources, which generates small amounts of power. Combining CeraChargeTM with other electronic components may lead to applications not yet realized by IoT devices. Commercialization of the world’s first solid SMD battery has triggered a major response, and we have been contacted by a large number of Japanese and international customers with various requests. To deal with a wider range of applications, we are now developing next-generation products with various capacities and sizes, such as the EIA0603 size (1.6 x 0.8 mm).
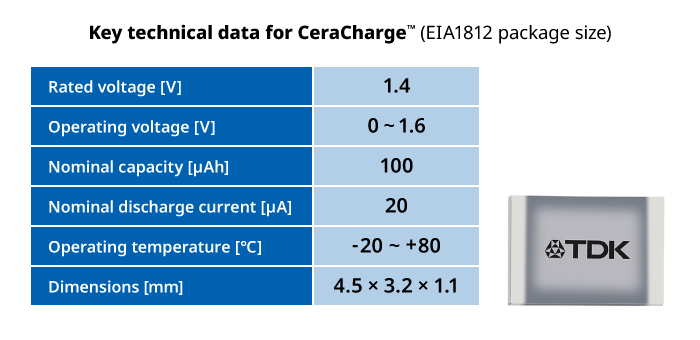
- Innovative Secondary Battery Using Solid-State Electrolyte Instead of Liquid Electrolyte
- Chargeable and Dischargeable All-Ceramic Battery that Can Be Mounted on a Board Together with Chip Components
- TDK Technology Realizes the World’s First Solid SMD Battery, CeraChargeTM
- Use Anticipated in Various Applications, Including IoT Devices
- Development Under Way for Next-Generation Products with Higher Capacity and Voltage